CarbonCure's technologies aim to make the concrete production process more efficient, unlocking value along the entire manufacturing chain and increasing profitability for concrete producers, regardless of their size or location.
Today, there are more than 650 CarbonCure systems operating at concrete plants around the world. Some are large nationwide brands, some are regional or state-wide, and others are one or two plant operations - but they’ve all seen the benefits of innovating with carbon mineralization and reclaimed water technology. In this article, we share experiences from several producers to demonstrate how easily—and successfully—CarbonCure can be adopted.
Conewago Manufacturing, Pennsylvania
Conewago is a family-run company founded in 1956 in Hanover, Pennsylvania. Conewago’s concrete plant delivers approximately 60,000 cubic yards (45,000 cubic meters) of concrete per year to various contractors throughout the Mid-Atlantic states.
Driven by the desire to deliver greener concrete to its community, Conewago decided to evaluate CarbonCure Ready Mix in early 2020 and never looked back. Today, CarbonCure is included in 98.87% of Conewago’s mix designs and their concrete maintains the same performance it is known for with a reduced carbon footprint.
During a recent webinar, Eric Smith, Sales Director at Conewago Manufacturing said, “CarbonCure just became our standard mix design. The only exceptions are some prescriptive specifications for the Department of Transportation, but we’re working with the CarbonCure team to change that.”
Conewago is fortunate to be geographically located next to excellent aggregate, so their concrete mixes don’t require as much cement content as other regions. With CarbonCure, Conewago still managed to reduce cement content by a further 5%—and this has delivered an excellent return on investment for the team.
"We didn’t embark on our CarbonCure journey for profitability reasons. However, we noted a 7.5% return on investment on our original target of just 1%,"
–said Jason Blase, President at Conewago Manufacturing.
The Conewago team encourages other producers to adopt CarbonCure and is even open to hosting producers at their plant to demonstrate how CarbonCure is working for them. “Any small to medium producer can do what we’ve done. Do not let your size stop you. CarbonCure has an outstanding onboarding process, robust testing and evaluation, an easy-to-execute installation process, and a team of technical and marketing partners assigned to your business to help you pursue new projects,” said Jason.
Trio Ready-Mix, Vancouver Island
TRIO Ready-Mix has been providing concrete to Southern Vancouver Island contractors, developers, landscapers, and homeowners for over 50 years. In 2018, TRIO designed a new concrete plant in Victoria, British Columbia. As an environmentally conscious company, TRIO began exploring ways to reduce the environmental footprint of its new facility and become the first to adopt CarbonCure Reclaimed Water.
The CarbonCure Technical Services and Support (TSS) Team was on the ground with Trio for the entire implementation and testing period. The team set up a small lab at Trio’s plant to run tests on the concrete, slurry, and water. Trio also conducted internal testing and hired a third-party testing company, EXL Engineering, to verify all slump, air, and strength tests.
Today, TRIO is replacing cement content by 3% with CarbonCure Reclaimed Water—and gaining up to an additional 4% reduction with CarbonCure Ready Mix.
CarbonCure Reclaimed Water is now used in 70% of TRIO’s mix designs, and over 75% of TRIO’s produced concrete. The team intends to add it to its high-performance 45, 50, and 60 MPa (6,527, 7,252, and 8,702 psi) concrete as it completes its optimization process before the end of the year.
When CarbonCure-treated reclaimed water is used in TRIO’s concrete mix, the savings average CAD $0.90 per cubic meter of concrete.
“Our initial motivator was environmental, not monetary. However, we have seen a great return on investment. The virgin cement replacement is where the true environmental and cost savings are, but the water treatment and savings on the cost of safe fines disposal are also significant.”
said Stephen Hay, General Manager of Trio Ready-Mix
Central Concrete Supply Co., West Coast U.S.
Central Concrete Supply Co., a northern California business unit of U.S Concrete, has been serving the San Francisco Bay Area for more than 70 years. Central Concrete has 19 plants across 11 locations, offering the largest capacity and depth of CarbonCure coverage in the Bay Area.
Central Concrete is recognized for leading the way in designing and delivering higher-performing concrete, while significantly reducing construction projects’ environmental impact with low-carbon mixes. In 2013, Central Concrete was the first company in the United States to offer Environmental Product Declarations (EPDs), and the first ready mix concrete supplier to produce an EPD for every product, online, in real-time. Four years later, Central Concrete took another big step toward low-carbon concrete by investing in CarbonCure.
In 2019, the first commercial application of CarbonCure on the West Coast was placed by Central Concrete at the New Academic Building at the University of California’s Hastings College of the Law. Shortly after, Central Concrete supplied concrete at the new LinkedIn Middlefield campus in Mountain View—the result of a conversation facilitated by CarbonCure’s executive team. The inclusion of CarbonCure provided an additional 5% carbon footprint reduction to an already sustainability-focused project, creating a total carbon saving of over 4.5 million pounds or 2,000,000 kilograms. Watch CarbonCure’s webinar with LinkedIn for more information on this project.
Thomas Concrete, Southeast U.S.
Thomas Concrete is a leading supplier of high-quality concrete in the Southeast United States (Georgia, South Carolina, North Carolina). Its parent company, Thomas Concrete Group, was established in Sweden in 1955, and the U.S. team has been serving customers for more than 30 years. A family-owned company, its environmental policy is at the heart of its identity.
Thomas Concrete has earned the reputation of being progressive, innovative, and sustainable so CarbonCure resonated with the team and they became the first producer to take part in the industrial trials of technology.
The results gave cause for excitement: an average 28-day strength increase of 10%! Today, CarbonCure is used at 48 of Thomas Concrete’s plants and the company sees great success both in terms of carbon reduction and cement replacement.
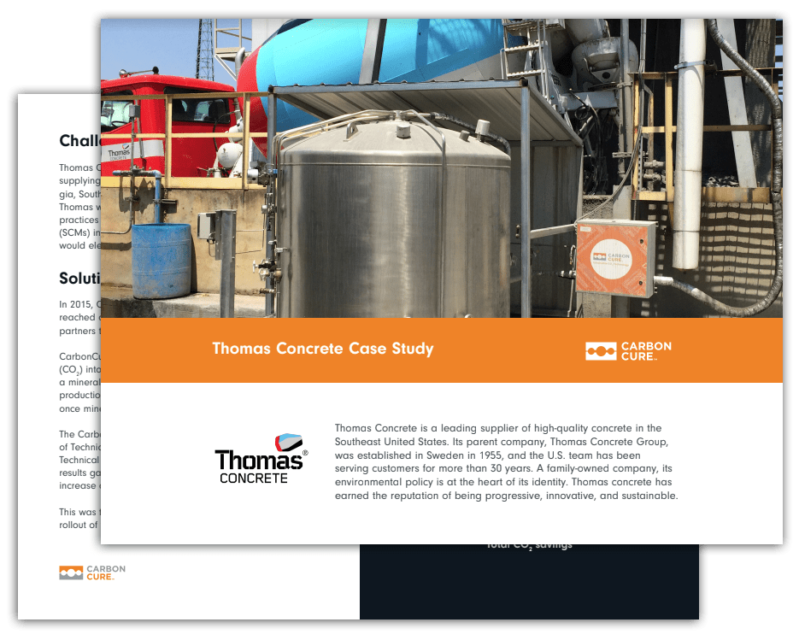
CarbonCure Fits Producers of All Sizes
Many regional or state-level concrete producers believe they do not have the resources to adopt new sustainable technologies like CarbonCure, but producers like Conewago and Trio prove that doing so is not only easy—it makes good business sense. Concrete producers like Thomas Concrete and Central Concrete demonstrate how CarbonCure delivers incredible value to larger producers, helping them win new business in the growing green building space and reduce cement content for more profitable mixes.
Our versatile technologies are being widely adopted for several reasons:
- CarbonCure can be retrofitted into any masonry, precast, or ready mix concrete producer’s existing operations with minimal disruption
- Our technologies enhance producers’ competitiveness by enabling them to deliver low carbon concrete and win new business in the growing green building space
- CarbonCure allows producers to cut cement content without compromising the quality of their concrete mixes for greater profitability
- CarbonCure’s Foundations Program offers concrete producers a proven roadmap to success with our technology
- Reducing CO₂ can provide producers with a new revenue stream thanks to the CarbonCure Carbon Credits program. CarbonCure producer partners receive regular checks for the amount of carbon they've saved by putting CO2 in their mixes and reducing the amount of cement in their concrete
If you’re interested in learning more about how CarbonCure could impact your concrete business, get in touch.
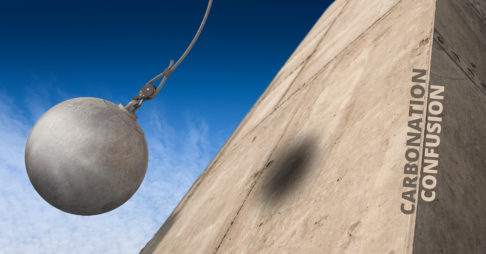
Razing a Common Misunderstanding: Early-Age Carbonation vs. Atmospheric Carbonation in Concrete