New technology for using reclaimed water may hold the key to water conservation
No water = No concrete.
Water is vital for the production of concrete. But drought and population growth are stressing this once abundant resource like never before. While concrete producers generally have diligent water management practices, they may need to fine-tune them even further to safeguard their water supply and ensure affordable concrete production. This may include re-examining their existing water conservation practices and adopting new technologies. One promising technology enables producers to reuse reclaimed water—without causing performance concerns—helping them become a virtually zero-waste operation.
Increased Demand Fuels Rising Costs
The strain on water resources stems from an increased demand on fresh water with population growth, combined with climate trends that have created droughts in many parts of the world. The current 22-year drought in California and the American West is the worst in the past 1,200 years. The Colorado River has dropped 20% since 2000 and seven adjacent states have been told to expect even more cutbacks on water allocation.
What was once seen as a low cost, abundant resource is now increasingly impacted by the law of supply and demand. According to a 2021 report by Bluefield Research, residential water rates have risen 43% in the United States from 2012 to 2021. A slightly earlier report from the U.S. Department of Energy indicates a similar trend for commercial water rates, which experienced an average annual increase of about 4.0%.
If concrete producers are not already paying for water, they may soon be. As the North America Ready Mix Concrete Association stated back in 2012, “Water is the new gold!”
Decreased Access and Increased Regulation in Water Scarce Regions
Unfortunately, it’s not just about how much water will cost, but the extent to which producers will have access to it. A report by McKinsey & Company predicts that by 2030, global demand for water will outstrip supply by 40% and that about half of the world’s population will live in water-scarce areas.
Concrete production currently accounts for almost 10% of global industrial water use.
It’s estimated that in 2050, 75% of the water demand for concrete production will likely occur in regions that are expected to experience water stress. The high proportion of water used for industrial and commercial purposes has not gone unnoticed by regulators.
In some regions in North America, governments have already put in regulations that prioritize water use for essential household needs and to protect aquatic ecosystems over industrial use.
Based on past concrete industry experiences in both North America and around the world, concrete producers can expect more scrutiny, regulations and restrictions to come.
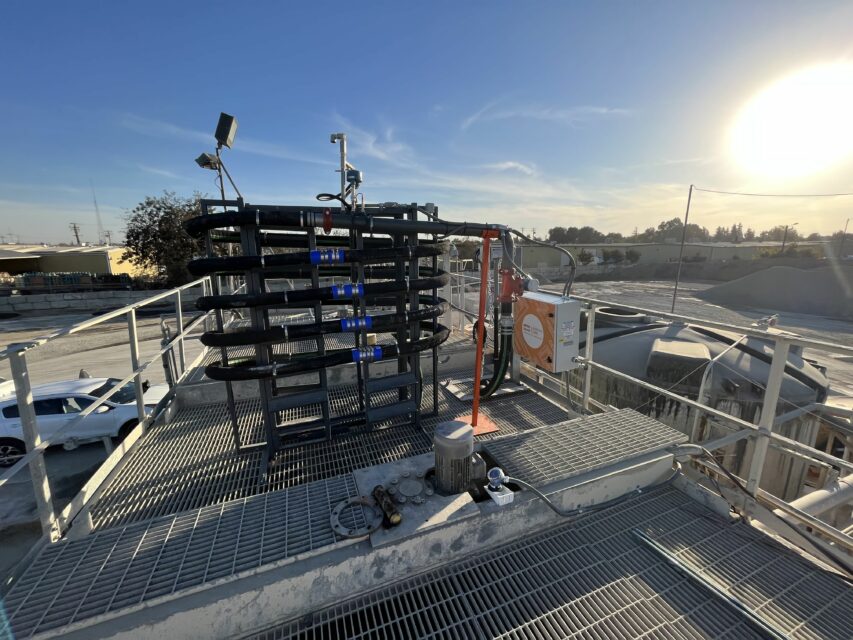
Fine-tuning Best Practices for Concrete Process Water Management
So what can concrete producers do to future-proof their operations to address water scarcity?
A review of literature found a number of measures and best practices, most of which have come from the concrete industry itself. These include:
- putting in better systems for measuring and monitoring water use
- aggressively monitoring systems to eliminate leaks
- optimizing mixes to prevent overuse of water
- minimizing the volume of wash water and process water
- installing reclaimers with agitated tanks and
- reusing as much reclaimed water as possible.
Map, Measure and Manage
If concrete producers are not already doing so, they can start by measuring their water use.
As management consultant Peter Drucker famously said, “If you can't measure it, you can’t manage it.”
Keeping track of the water used in batching is not difficult for most producers. They know their mix designs and track the volumes they’ve produced. The bigger challenge is measuring and managing the water used outside of production for washing out concrete truck drums, washing down equipment and keeping their sites clean.
To help with measurement and management, the Cement Sustainability Initiative (CSI) of the World Business Council for Sustainable Development developed a Protocol for Water Reporting, which can be used in ready mix concrete operations.
According to a 2021 CemNet article, large concrete producers are already mapping their water resources and taking steps to show regulators that they are acting now to reduce water use and are planning further reductions for the future. For example, it reports that Swiss multinational Holcim is aiming for a 15-percent reduction in water use for ready mix by 2030 from 2018 levels.
Eliminate Leaks
While not all producers have the resources to map, measure and monitor all their water use, producers of any size can monitor their systems to eliminate leaks. In its Best Management Practice for Ready Mix Concrete Process Water, the California Construction and Industrial Materials Association (CalCIMA) recommends observing all means of process water conveyance: pumps, piping, swales, curbs and berms. It also recommends watching surrounding soil surfaces for signs of overflow and to look for process water staining, erosion and sediments.
Optimizing Mixes
On average, water makes up about 18% of the concrete ready mix itself, not including the water used in other processes. The proportion of water used in batching can vary based on the mix design, temperature and humidity.
Some producers reliably use less at 160 liters per cubic meter, while others are able to reduce their mix water down to 120 liters per cubic meter, depending on the temperature.
One of the positive changes in recent years is a move away from prescriptive specifications that dictate how much water is used in mix designs to guarantee the pump-ability and workability of fresh concrete. The industry is increasingly using performance specifications, including those based on slump and air content. This enables mixes to be a little leaner on water as long as the reduction doesn’t come at the expense of workability.
Minimizing Washouts and Process Water
When process water is also accounted for, water makes up 30% of the total resources used in concrete production. But averages can hide a wide variance between producers at the low and top end of water use. Past surveys have shown process water use ranging from 35 to 515 liters per cubic meter. According to the Portland Cement Association’s Environmental Life Cycle Inventory of Portland Cement Concrete, the three major factors–other than the mix–that influence water consumption are the type of plant, plant location and plant size.
- Type of plant: Central mix plants load wet product into concrete trucks tend to require less wash-off water than transit mixer operations that load out a dry material.
- Plant location: Rural plants with longer average hauls to job sites are more likely to use transit mixers than urban plants that have shorter hauls.
- Plant size: Larger plants, particularly those in urban areas, are more likely to have water-recycling systems.
Outside of those given factors, CalCIMA’s Best Management Practice for Ready Mix Concrete Process Water offers a number of tips for minimizing the use of potable water, reducing any excess water used in washouts and minimizing the overall volume of process water generated. Best practices for accomplishing this include:
- using high pressure, low volume hoses for washout, decreasing the volume of water needed to clean the concrete truck drums and equipment
- conveniently locating water shut-off valves to prevent accidental overfilling
- installing overhead spray bars with high-pressure, low-volume water flow to reduce the amount of water used for truck rinsing
- collecting stormwater on site, in regions where this is practical, and using that for washouts
“Here in the Pacific northwest, we’ve become adapted to taking advantage of what falls out of the sky.”
- emptying trucks before washout, creating blocks from returned concrete so there’s less washout required
- rinsing trucks only when required, once a day at the end of the day, or as operationally necessary for changing mix designs, concrete colors or to limit build-up.
- limiting washout water to what is operationally necessary: about 150 to 300 gallons (568 to 1136 liters) for each drum washout, understanding that too much water in the drum can actually reduce the cleaning action of the tumbling water in the drum
- rocking out drums, using aggregate or sand instead of water to scrub the drum clean, and to reduce the amount of drum chipping needed
- re-using process water for washouts, whether it’s clarified water from pits or reclaimed water from tanks.
Most concrete producers are very good at running their washout systems in a closed loop. However, solids build up in pits or tanks and must eventually be removed, taking water with them. Solids hauled away typically have an average moisture content of 20%, but vary between 15 to 30%, depending on the method of separation.
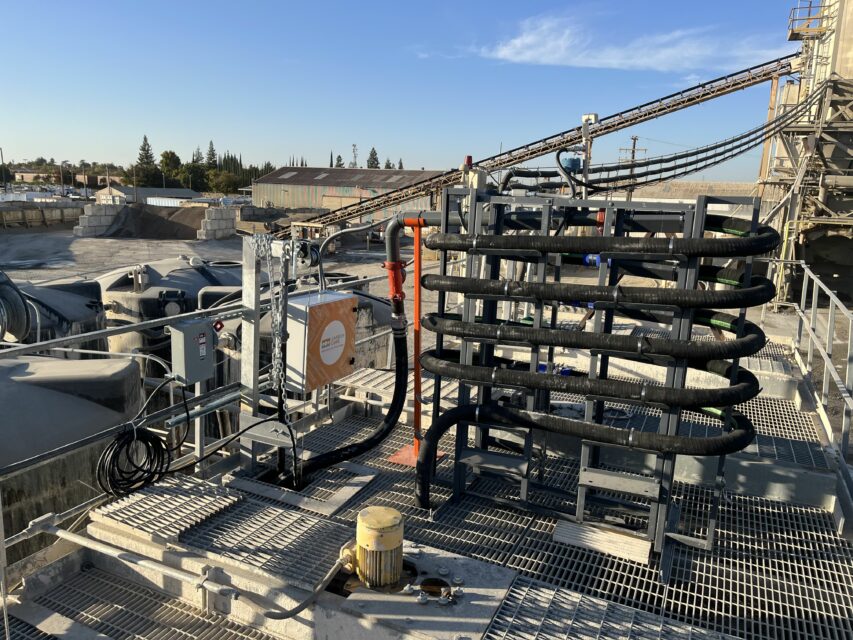
Consider Installing and Using a Reclaimer with an Agitated Tank
There are many different reasons why producers choose a pit system or a reclaimer with an agitated tank. When you look at the two options from the perspective of water use, reclaimers with agitated tanks are about twice as effective at separating water from fine aggregates. Typically, the solids disposed from a pit have an average moisture content of about 30%, while solids disposed separated out from an agitated tank using a filter press hold about 15% moisture.
Using a reclaimer with an agitated tank can save an estimated 70% of the water used in concrete production. While pit systems can also save water for reuse in washouts, they are subject to water loss due to evaporation. For most concrete producers, evaporation is used purposefully to reduce the weight of the solids removed. While producers don’t have to haul away as much water with their solids or as much excess water for treatment, they’re also not able to reuse water that has evaporated – it’s a lost resource.
In Europe, where environmental considerations are a higher priority and space is limited, about 50% of producers have adopted reclaimers with agitated tanks. Industry experts estimate that less than 3% of producers in North America have or use reclaimers with agitated tanks. But that may be changing. Growing concerns over water scarcity and water protection are expected to increase the adoption of reclaimers with agitated tanks in both continents. In many markets in Europe, one of the requirements for certification of new plants is that they have recycling and wastewater management plans that include a full-spectrum reclaimer.
Reuse Process Water in Mixes
Process water can be reused to reduce the use of freshwater. Traditionally, in order to reuse process water, producers have had to use some form of clarification, filtration, retardation and/or dilution to reduce the impact of the slurry on the quality of their concrete.
Some producers have developed certain mixes that can work with the traditional reclaimed water. With these select mixes, at best there’s a 50-percent reduction in freshwater use. Other producers avoid reusing reclaimed water at all because of unpredictable results on the concrete.
Any or all excess reclaimed water is typically clarified using a weir system to remove suspended solids, neutralized and then discharged into the local environment or into municipal wastewater treatment systems or, alternatively, hauled away for treatment.
However, there is another option that enables producers to optimize their concrete reclaimer and reliably use reclaimed water without any negative impacts on their concrete’s fresh or hardened properties. This makes reclaimers with agitated tanks significantly more effective in saving water.
ASTM 1602 permits non-potable water to be used as mixing water in concrete, allowing producers to exceed the as long as the concrete performance requirements for compressive strength and time of set are met.
Similarly, the European code for concrete mix water, EN 1008 [4] permits greater quantities of solids if satisfactory performance in concrete can be demonstrated.
ASTM 94 While a maximum water-cement ratio (w/c) or water-cementitious materials ratio (w/cm) can be specified, C94 doesn’t contain provisions for doing this directly.
New Technology for Reusing Reclaimed Water
While the #1 way to reduce water use is to install a reclaimer with an agitated tank, the challenge has always been what to do with the excess reclaimed water. Are producers really “saving” water if they end up hauling it away for treatment or disposal? For true savings – both ecologically and financially – producers need to be able to use the vast majority of reclaimed water without compromising the quality of their concrete or creating new hassles.
The latest innovation from CarbonCure Technologies – CarbonCure Reclaimed Water – makes that possible and has producers rethinking their use of reclaimed water.
CarbonCure has a suite of technologies that employ carbon mineralization to produce low carbon concrete in hundreds of plants around the world. CarbonCure Ready Mix technology injects captured CO2 into concrete as it is being mixed, where it reacts with the cement and is chemically converted to a mineral. The mineralization process enables a reduction of cement content, without impacting its performance or properties.
Similarly, with CarbonCure Reclaimed Water, the CO2 is injected into the slurry from a unit installed on top of the reclaimer system’s agitated tank. The CO2 reacts with the cement in the slurry, producing that same mineral as an ultrafine suspended solid. The mineral acts as a binder, reducing the amount of cement needed. The reaction of CO2 is monitored in real-time using specific measurements to better understand the composition of the reclaimed water. This enables its use as a stable, reliable, value-added product, rather than an inconsistent nuisance affecting concrete performance.
By using a reclaimer with an agitated tank, producers are already saving about 70% of the water present in returned concrete along with the washwater. With the addition of CarbonCure Reclaimed Water, producers are able to save about 90% of the water, reusing it in new batches.
“Instead of trucking that wet solid away, you're using it back in the concrete mix. That’s where the 20% water savings comes from,” says Travis Janke, Senior Director of Product Development.
Added value and economics
CarbonCure Reclaimed Water also adds value by enabling the cementitious fines in the slurry to be reused. When used as a stand-alone technology, it can reduce virgin cement use in mixes by about 3-5%. When combined with CarbonCure Ready Mix the total reduction of virgin cement climbs to 8-10%, providing significant savings on material costs.
“Everyone's going to be washing out their trucks to some extent. The key question is, What are they doing with that water once they wash it out? Are they just trying to process that water and use it again? Or are they extracting the full value from it?” asks Kevin.
The full value includes more than just the material savings on virgin water and cement. The removal and reduction of CO2 in the process also provides environmental and economic benefits. Every ton of CO2 removed or reduced through CarbonCure’s technologies can produce high-quality, verified carbon credits that can be sold to companies who have climate goals.
Through the CarbonCure Carbon Credit Program, CarbonCure shares the revenue from carbon credits with producers, making it feasible to adopt the technology and generate a new revenue stream while producing lower carbon concrete to meet the growing demand. This not only pays for the CarbonCure technology subscription, but in some scenarios could potentially recoup the cost of an agitated reclaimer tank in as little as one year.
Using CarbonCure Reclaimed Water with an existing or new agitated tank reclaimer could be a viable solution for concrete producers whether they are in regions currently experiencing water stress or not. Considering the current trends, it may also be a prudent investment to help producers future-proof their ready mix concrete operations.