With more focus than ever on embodied carbon in construction, demand for low-carbon building materials is increasing. This demand is driven by private project owners, designers, and government agencies committed to addressing climate change.
SE2050, Architecture2030, and the Carbon Leadership Forum are just some examples of the commitments that the design community has made to decarbonize the construction industry. As such, the design industry is actively seeking low-carbon materials to use in new construction projects.
In an ideal world, high-quality environmental product declarations (EPDs) would be universally available to provide designers and specifiers the information they need to make informed decisions about these materials. However, EPDs are not widely available for concrete products yet.
Given the urgency to deliver low-carbon concrete today, it’s important to not let perfection get in the way of progress. In a recent webinar, Michael Cropper, Structural Engineer at Thornton Tomasetti, and Jennifer Wolf, Sustainable Program Manager at Sustainable Building Partners shared their experiences working with partners across the design and construction industry—from general contractors to concrete producers—to collaborate, share project data, and deliver low-carbon building materials—even in the absence of EPDs.
Delivering Low-Carbon Concrete Without EPDs
EPDs were designed to provide a consistent, data-backed measurement of the impact of manufactured products. They quantify and report the environmental impacts of materials covering a defined portion of the product’s lifecycle.
EPDs were not meant to be comparative. For the purposes of estimating embodied carbon reductions, however, data in EPDs is compared to a baseline value to measure the reduction of carbon. If a lack of EPDs exists, there is no baseline data to compare against. This means that in many regions, alternative strategies must be used.
Thornton Tomasetti worked on a large commercial office project in the DC region with over 150,000 cubic yards (114,683 cubic metres) of concrete. There were no EPDs available to refer to. Instead, the team collaborated with the project owner, architect, sustainability consultant, and contractor to implement a simple but effective approach to reduce embodied carbon by 30%.
While EPDs offer key data points, the design community can still access some of the data from manufacturing processes to make informed decisions about low-carbon building materials. As described below, the keys to doing so are found in:
- Cross-industry collaboration
- Benchmarking tools
- Performance-based specifications
1. Cross-Industry Collaboration
The design community has made serious commitments to move the needle on climate change and wants to collaborate with industry players to help them achieve their goals.
“Start early with clear goals and be prepared to collaborate across the entire design team—contractors, subcontractors, concrete producers, mix designers.”
Michael Cropper, Structural Engineer, Thornton Tomasetti
Reducing embodied carbon in concrete structures is a combination of design choices and the makeup of the concrete mix designs used on the project. According to Michael, “Gaining meaningful embodied carbon reductions can't be done simply by cherry-picking particular tips and strategies—the project team all needs to work together.”
This makes sense. Selecting overly conservative loads or thicker, less efficient slabs will negate any impact made by a concrete producer to reduce cement content or adopt carbon mineralization technologies. Good design that meets the project’s needs is always the foundation for low-carbon success.
By working together on project roadmaps and defining embodied carbon goals upfront, project teams can also create benchmarks and define ways to unlock data to inform decisions and prove the impact of their efforts as the project progresses. Having a plan for success from project inception that is understood and supported by all project partners increases the chances of successfully limiting embodied carbon.

2. Benchmarking Tools
Early in any project design, the team should begin tracking and evaluating embodied carbon so it can benchmark progress. As described, industry benchmarks and available local EPDs are great resources for project teams to understand what “good” performance looks like when it comes to embodied carbon. By considering local and industry benchmark data, project teams have a standard point of reference to compare their own efforts to. Local data may also help project teams understand what the practical and technical limits are for their carbon reduction goals.
What if your region doesn’t have EPD data? First, start with the industry baseline. Then, consider ways that EPDs could be generated as part of your project.
“We feel it's important to encourage the creation of EPDs for a concrete mix design—it gives us more data that we can then use to narrow in on that benchmark,” said Jennifer. “However, in the absence of local EPDs, there are plenty of valuable resources to evaluate and set reasonable targets.”
Benchmarking with EPDs:
- Carbon Leadership Forum EC3 Tool: database of EPDs
- NRMCA: regional EPDs
- Portland Cement Association EPD: industry-wide cement EPD
Benchmarking without EPDs:
- ZGF powered by Tally: LCA tool that calculates the cradle to grave impacts of concrete
- Beacon by Thornton Tomasetti: embodied carbon measurement tool
Once the benchmarking is established, the simplest way to move the needle on embodied carbon is to use performance-based specifications.
3. Performance-Based Specifications
Prescriptive specifications create barriers that inhibit innovation and performance. The practice of writing prescriptive specifications, in particular a minimum cement content requirement, originated decades ago when concrete production quality control standards were not as robust as they are today.
According to Jennifer, concrete specifications should encourage innovative solutions backed by test data.
“In the future, we expect to see global warming potential goals and embodied carbon goals included in concrete specifications.”
Jennifer Wolf, Sustainable Program Manager, Sustainable Building Partners
Since concrete suppliers are the experts in their field, it’s best for designers to focus on concrete performance. By setting the required strengths and other parameters from the design side (target embodied carbon reductions), concrete suppliers have the freedom to bring the best solutions forward to meet project needs. “Let the experts in their field work within the other construction-related constraints to reduce carbon content,” said Michael.
Conclusion
In regard to embodied carbon, there is a lot of traction and urgency in the industry which has already resulted in measurable improvements.
As the design community and suppliers set out to meet their respective commitments to decarbonize the built environment, EPDs are important resources to guide their decision-making. But their lack of availability in some regions does not need to be a barrier to change. The industry can't afford to wait for "perfect.”
According to Jennifer, you have to start somewhere! Collaboration, benchmarking, and performance-based specifications are great foundations to build on and can result in significant reductions in carbon emissions and a transformed built environment.
For more information, watch the on-demand webinar Specifying Low-Carbon Concrete Without EPDs.
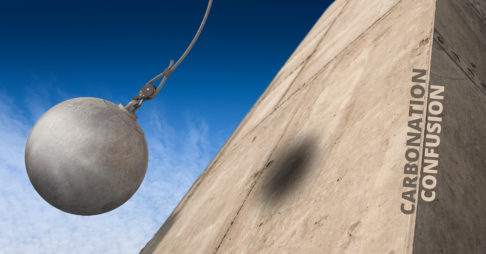
Razing a Common Misunderstanding: Early-Age Carbonation vs. Atmospheric Carbonation in Concrete